Home
>Machinery & Industrial Parts » Machinery » Building Material Machinery » Glass Production Machinery
CHANGZHOU SINOMAC MACHINERY TECHNOLOGY CO., LTD.
Business units
ChinaVIP0Audited Supplier
Products: Composite Autoclave , Glass Autoclave , Medical Waste Disposal Autoclave , Laminated Autoclave , Vulcanization Autoclave , Rubber Autoclave , Wood Autoclave , Laminated Glass Line , Wood Treatment Autoclave , Carbon Fiber Autoclave
Response Time: within 24 hours
Response Rate: 100%
+ Follow
View Shop
Chat Now
Related Products
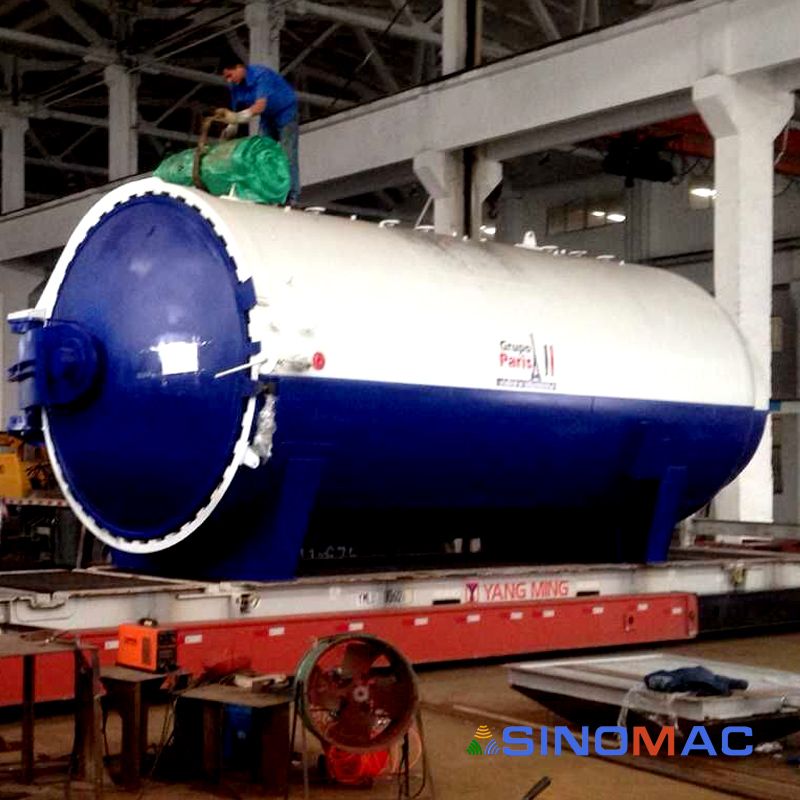
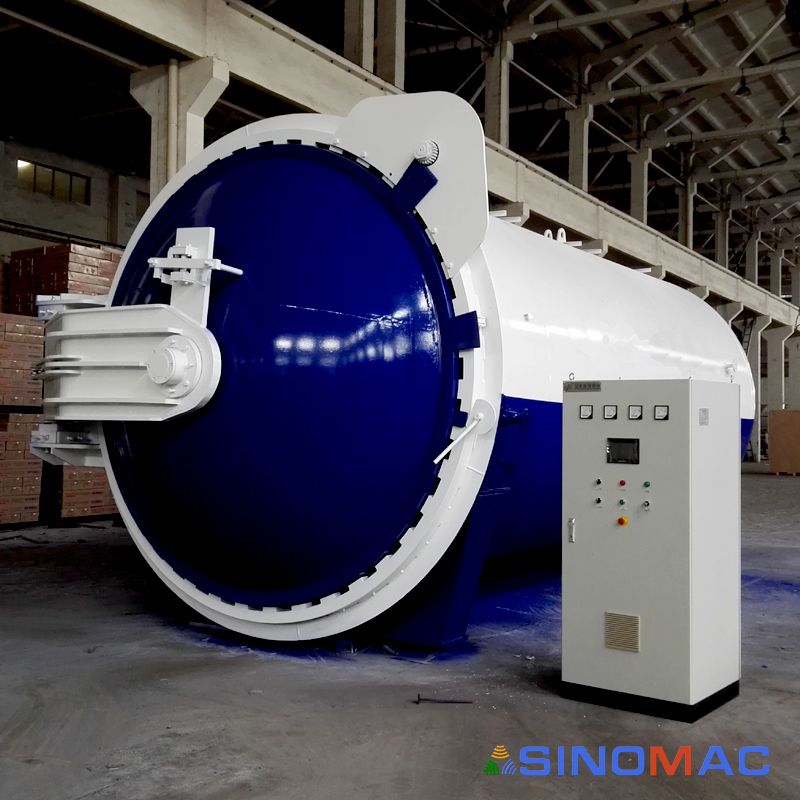
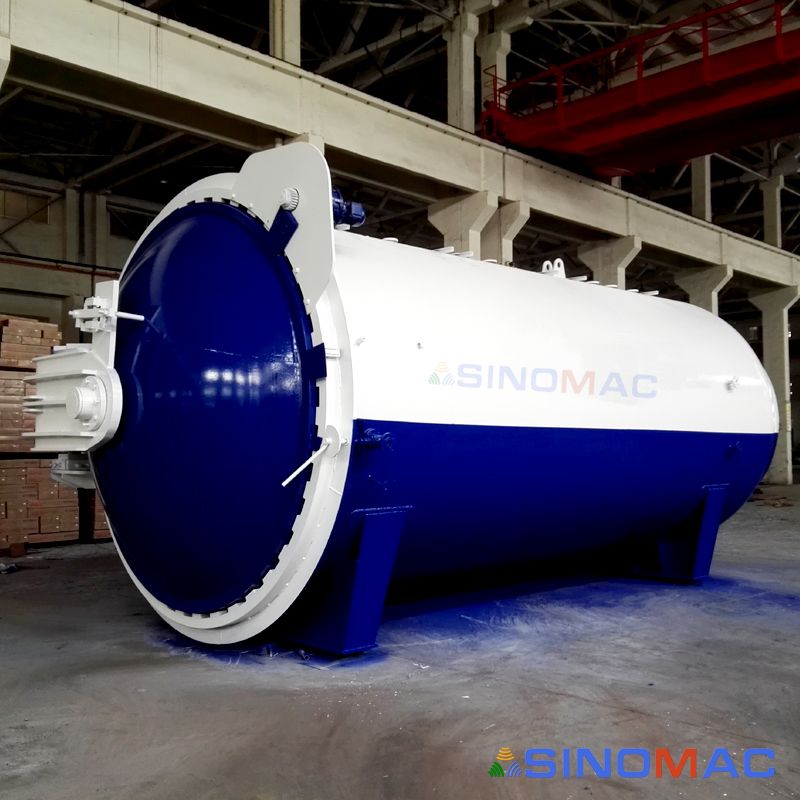
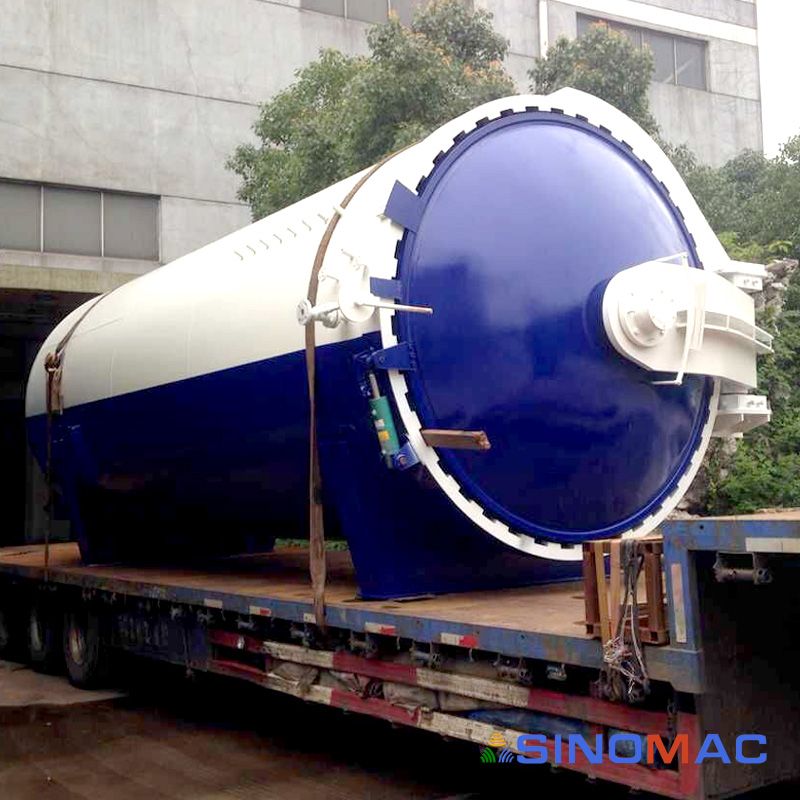
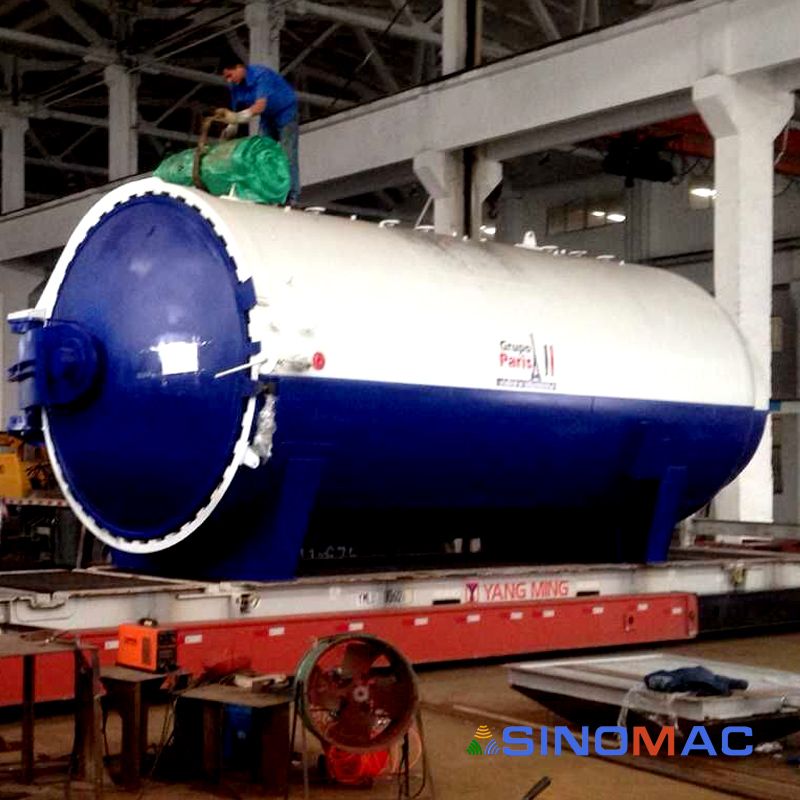
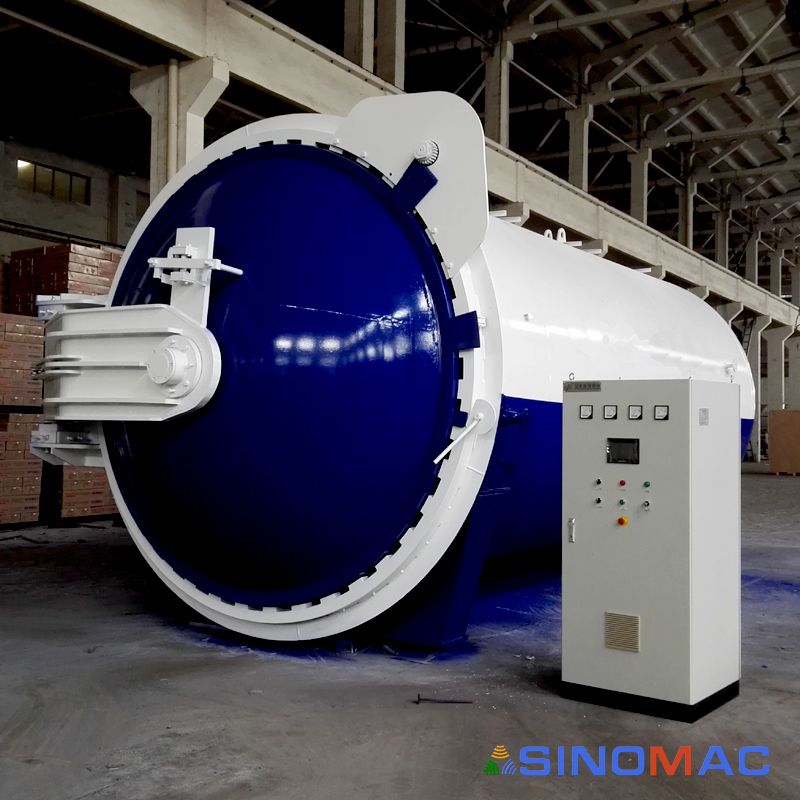
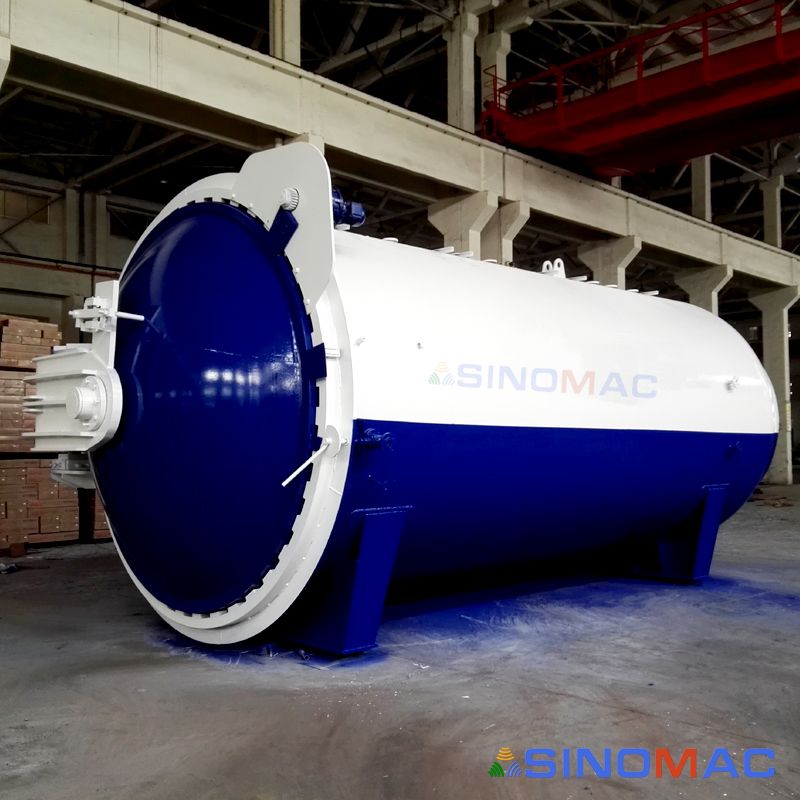
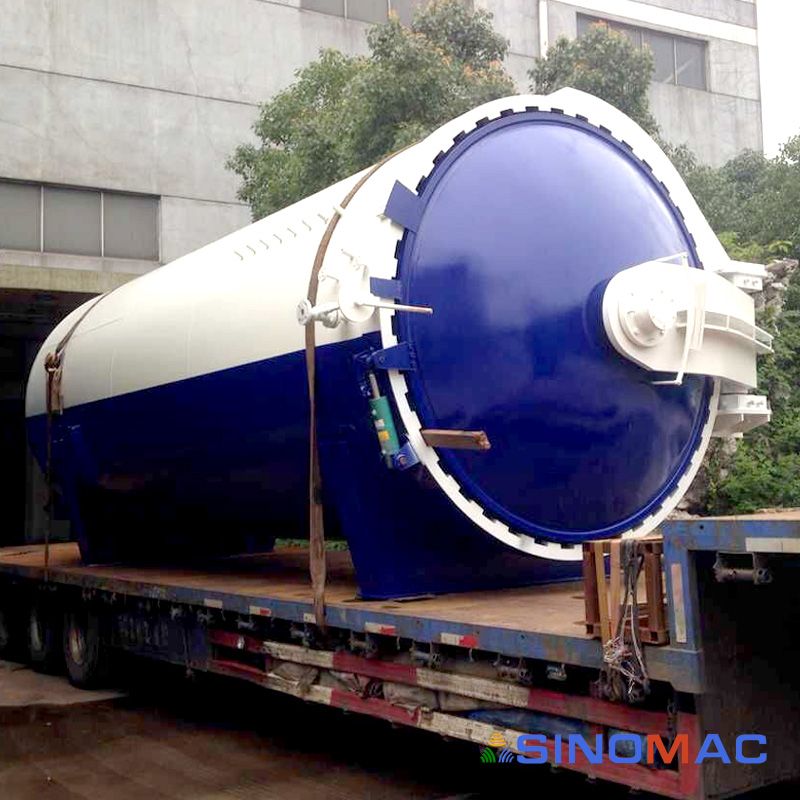
Add to wish list
+ Add a New List
CE Certified Laminated Glass Machine for Building Glass (SN-BGF3060)
$85000.00 /set
Product Details
Transaction Comments
Basic Info
- Model NO.: SN-BGF3060
- Automatic Production Line: Laminated Glass Line
- Automation: Automation
- Rhythm: Flow Production Line
- Size: 3000X6000mm
- Max. Glass Size: 2650X6000mm
- Design Temperature: 160 ºC
- Control Mode: PLC+Him/PC
- Working Medium: Compressed Air
- Trademark: SINOMAC or OEM
- Specification: SN-BGF3060
- HS Code: 84752919
- Transmission Type: Flexible
- Certification: ISO, CE, ASME/PED
- Flexible Production: None
- Production Scope: Product Line
- Material: Q345r Carbon Steel
- Design Pressure: 1.5 MPa (15bar)
- Heating Mode: Electric/Natural Gas/Thermal Oil
- Control Software: Tpc (Thermal Processing Control )
- Voltage: 380/400/415/440/600VAC
- Transport Package: Standard Package
- Origin: Changzhou, Jiangsu, China
Product Description
Note: With many years of experience and development, SINOMAC has obtained the full capacity to offer complete and professional Turnkey Projects for you. It is quite worhty of your choice. Welcome to vist and consult.
Usage of SINOMAC Glass Autoclave
In two or more pieces of glass sandwiching a polymer plastic film material, after the initial pressing and then into the autoclave was fully heated, pressurized, and got a kind of synthesis of glass products, known as the laminated safety glass. Laminated products consisting of various raw materials, particularly the process of intermediate membrane in autoclave is important to obtain a high quality of the products. In fact, SINOMAC glass autoclave's role is to ensure access to the product quality requireents, its stabments, ility and process to ensure product to achieve and maintain high standards of quality requirements.
SINOMAC glass autoclave is widely used in the field of Architecture, Automotive and Solar.
General Features and Working Curve
The whole operation process of SINOMAC Glass Autoclave has 6 segments. Pre-heating and pre-pressing segment, first segment of temperature and pressure keeping, heating and pressurizing segment, second segment of temperature and pressure keeping, cooling segment, air exhaust segment. During the whole process, temperature and pressure in all segments will be monitored by HIM or PC, and the operation process will be realized by our exclusively developed TPC(Thermal Processing Control)software which is based on PLC control system to ensure the full automatic operation.
Technical Description
1. Quick opening door
- The whole system consists of three parts: A pair of gear flange, driven devices and seal ring.
- Hydraulically operated door opening and closing.
- The seal ring is made of silicon rubber.
2. Insulation system
- Insulation: Inner insulation
- Insulation material: Aluminium silicate+ rock wool
- Internal sheet metal: Stainless steel, 0.8 mm
- Insulation thickness: 80mm
3. Floor supports and rails
- Rail loading: 20,000kg, Increased loading can be offered optionally.
- Rail type: Unequal angle steel
- Floor loading: 400kg, Increased loading can be offered optionally.
- Form of floor supports: Mild Steel Checkered Plate
4. Heating system
- The heating system consists of the main heating zone and auxiliary heating zone, the heating element located in the rear and sides of the wind duct to ensure uniformity of temperature during the heating process.
- Electric heating via inconel tubular heaters
5. Cooling system (heating exchange)
- The main heating exchanger is made of Aluminum finned tube, which located in the rear of the autoclave.
- The auxiliary cooling system is made of Aluminum finned tube. Exchanger mounted in side wall for easy system maintenance.
6. Forced convection system
- Parameters of circulating fan
Power: 22 KW,
Connecting format: Direct-connected,
Rated rotate speed: 960 r/min(400V/50HZ),
Fan wheel: 7# centrifugal impeller,
Wind pressure: 1100Pa,
Flowrate: 14400M3/h.
- Shaft sealing
Mechanical seal, silicon carbide - graphite materials as static and dynamic ring seal, bearings with high-temperature series.
7. Temperature monitoring components
- Air temperature thermocouples: 3, PT100, including HMI monitoring, data-acquisition, and control
- Hi-limit thermocouple: 1, PT100, including HMI monitoring/control.
8. Vacuum system
Vacuum source ports: 6 total
9. Control System
- Control System is developed based on the research and development toward glass processing industry, including the PLC central controlling part, touch screen (HIM) operation system and network. The operation of the whole system is based on the exclusive developed TPC (Thermal Processing Control )software.
- It can insert or save the production technique process, display the pressure and temperature curve anytime; And its paperless record function can realize record, save and check of technique curve and process parameters.
- Advanced TPC control software makes the controlling technique during the process of temperature waiting for pressure, pressure waiting for temperature possible to ensure the simultaneous effect of temperature and pressure according to the settled technique curve, and it also has over-temperature and overpressure alarm and various safety protection functions.
- Customer can operate register, login and typing in product information, and realize intranet or remote control.
- It can realize data output, printing, analyzing requirements to improve product quality.
Foundation and Installation
Autoclave Specification
Professional Workshop
From the SINOMAC team, with 15 years of experience.
Usage of SINOMAC Glass Autoclave
In two or more pieces of glass sandwiching a polymer plastic film material, after the initial pressing and then into the autoclave was fully heated, pressurized, and got a kind of synthesis of glass products, known as the laminated safety glass. Laminated products consisting of various raw materials, particularly the process of intermediate membrane in autoclave is important to obtain a high quality of the products. In fact, SINOMAC glass autoclave's role is to ensure access to the product quality requireents, its stabments, ility and process to ensure product to achieve and maintain high standards of quality requirements.
SINOMAC glass autoclave is widely used in the field of Architecture, Automotive and Solar.
General Features and Working Curve
The whole operation process of SINOMAC Glass Autoclave has 6 segments. Pre-heating and pre-pressing segment, first segment of temperature and pressure keeping, heating and pressurizing segment, second segment of temperature and pressure keeping, cooling segment, air exhaust segment. During the whole process, temperature and pressure in all segments will be monitored by HIM or PC, and the operation process will be realized by our exclusively developed TPC(Thermal Processing Control)software which is based on PLC control system to ensure the full automatic operation.
Technical Description
1. Quick opening door
- The whole system consists of three parts: A pair of gear flange, driven devices and seal ring.
- Hydraulically operated door opening and closing.
- The seal ring is made of silicon rubber.
2. Insulation system
- Insulation: Inner insulation
- Insulation material: Aluminium silicate+ rock wool
- Internal sheet metal: Stainless steel, 0.8 mm
- Insulation thickness: 80mm
3. Floor supports and rails
- Rail loading: 20,000kg, Increased loading can be offered optionally.
- Rail type: Unequal angle steel
- Floor loading: 400kg, Increased loading can be offered optionally.
- Form of floor supports: Mild Steel Checkered Plate
4. Heating system
- The heating system consists of the main heating zone and auxiliary heating zone, the heating element located in the rear and sides of the wind duct to ensure uniformity of temperature during the heating process.
- Electric heating via inconel tubular heaters
5. Cooling system (heating exchange)
- The main heating exchanger is made of Aluminum finned tube, which located in the rear of the autoclave.
- The auxiliary cooling system is made of Aluminum finned tube. Exchanger mounted in side wall for easy system maintenance.
6. Forced convection system
- Parameters of circulating fan
Power: 22 KW,
Connecting format: Direct-connected,
Rated rotate speed: 960 r/min(400V/50HZ),
Fan wheel: 7# centrifugal impeller,
Wind pressure: 1100Pa,
Flowrate: 14400M3/h.
- Shaft sealing
Mechanical seal, silicon carbide - graphite materials as static and dynamic ring seal, bearings with high-temperature series.
7. Temperature monitoring components
- Air temperature thermocouples: 3, PT100, including HMI monitoring, data-acquisition, and control
- Hi-limit thermocouple: 1, PT100, including HMI monitoring/control.
8. Vacuum system
Vacuum source ports: 6 total
9. Control System
- Control System is developed based on the research and development toward glass processing industry, including the PLC central controlling part, touch screen (HIM) operation system and network. The operation of the whole system is based on the exclusive developed TPC (Thermal Processing Control )software.
- It can insert or save the production technique process, display the pressure and temperature curve anytime; And its paperless record function can realize record, save and check of technique curve and process parameters.
- Advanced TPC control software makes the controlling technique during the process of temperature waiting for pressure, pressure waiting for temperature possible to ensure the simultaneous effect of temperature and pressure according to the settled technique curve, and it also has over-temperature and overpressure alarm and various safety protection functions.
- Customer can operate register, login and typing in product information, and realize intranet or remote control.
- It can realize data output, printing, analyzing requirements to improve product quality.
Foundation and Installation
Autoclave Specification
MODEL#SN-BGF3060 GLASS AUTOCLAVE_TECHNICAL PARAMETER | |||
No. | Description | Unit | Specifications and Parameters |
1 | Inner Diameter | mm | 3000 |
2 | Working Length | mm | 6000 |
3 | Max. Glass Size | mm | 2650X6000 |
4 | Autoclave Track Distance | mm | 1000 |
5 | Track Height | mm | 480 |
6 | Design Pressure | Mpa | 1.5 |
7 | Design Temperature | ºC | 160 |
8 | Working Pressure | Mpa | 1.3 |
9 | Working Temperature | ºC | 150 |
10 | Safety Valve Exhaust | Mpa | 1.4 |
11 | Working Medium | --- | Compressed Air |
12 | Heating Mode | --- | Electric(Convection+Radiation ) |
17 | Heater | --- | Inconel Tubular Heaters |
18 | Heating Power | KW | 198 |
19 | Circulating Fan Motor Power | KW | 22 |
20 | Thermocouple type | --- | K or PT100 |
21 | Air Temperature Thermocouples | Piece | 3 |
23 | Pressure Transducer | Piece | 1 |
24 | Vaccum Lines | Piece | 6 |
25 | Control Mode | --- | PLC+PC |
26 | Control Software | --- | Thermal Processing Control (TPC) |
23 | Insulation | --- | Internal |
24 | Supporting Air Tank | M³ | 3 |
25 | Working Environment Temperature | ºC | Min. -20ºC, max.+45ºC |
26 | Working Environment Humidity | --- | < 60% |
27 | Power Supply | --- | 220/380VAC, 3P+N+PE, 50/60Hz |
28 | Weight | KG | 21490 |
From the SINOMAC team, with 15 years of experience.
Other products from this supplier
Back to top